Have you ever watched your 3D print, carefully prepared and positioned, slowly sink into the resin vat? This frustrating occurrence can turn a promising project into a sticky mess. But don’t worry, we have solutions to prevent this and save your prints.
Why does this happen? It’s often because the print isn’t adhering properly to the build plate. This adhesion problem can be caused by several factors, so let’s explore them and find ways to fix them.
Level Up Your Build Plate Game
The foundation of a good print starts with a properly leveled build plate. If your plate is off-kilter, even by a smidge, your print might decide to go for a swim. Here’s a quick leveling hack:
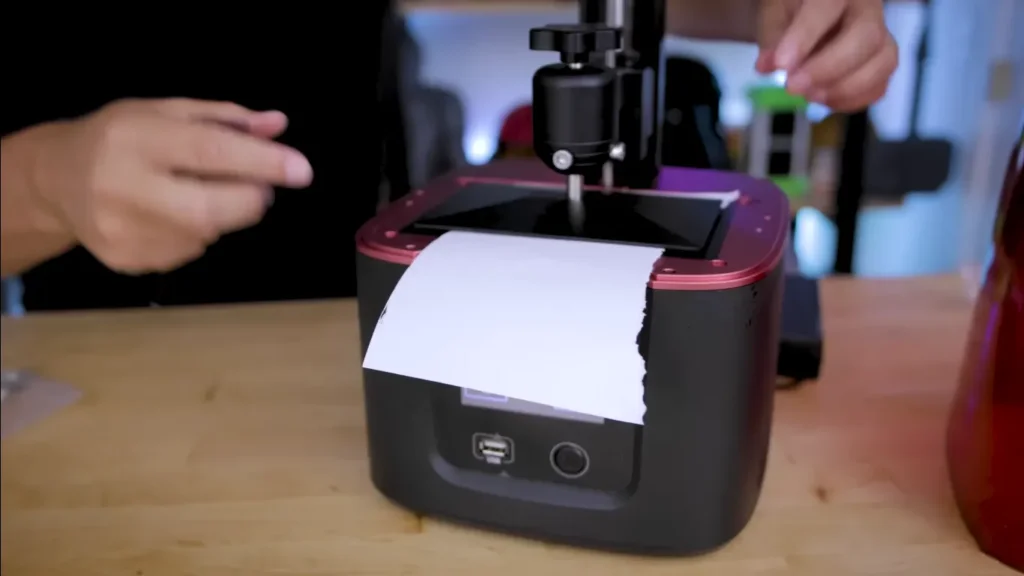
- Tighten that plate down.
- Grab a piece of paper and slide it under each corner.
- If the paper moves freely, your plate’s not snug enough. If it doesn’t budge at all, you’re golden.
Remember, You don’t need to re-level often. Only do it if your prints are uneven or if you’ve accidentally bumped the build plate.
Sand That Plate (But Not Too Much)
Sometimes, Your build plate will need a little bit of help to have the resin stick. All you need to do is lightly sandpaper the plate with very high-grit (600-1000 grit) between two layers. Want the plate to be scratched, but remember this is simply creating surface texture.
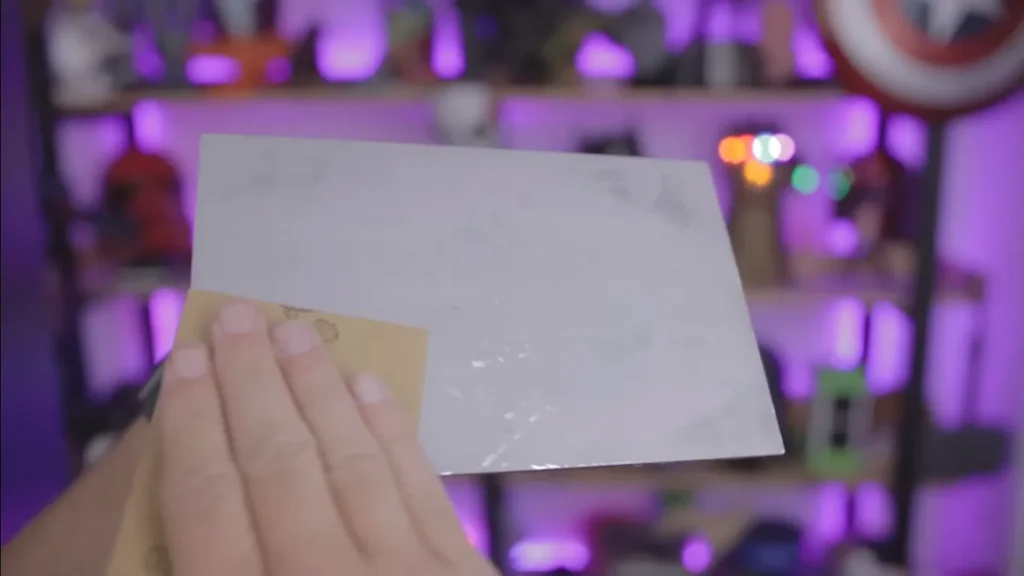
Crank Up the Bottom Exposure
If your prints are still pulling a Houdini and disappearing into the resin, it’s time to tweak your slicer settings. The bottom exposure time is your best friend here. This setting determines how long the first few layers are cured, and a longer exposure means a stronger grip on the build plate.
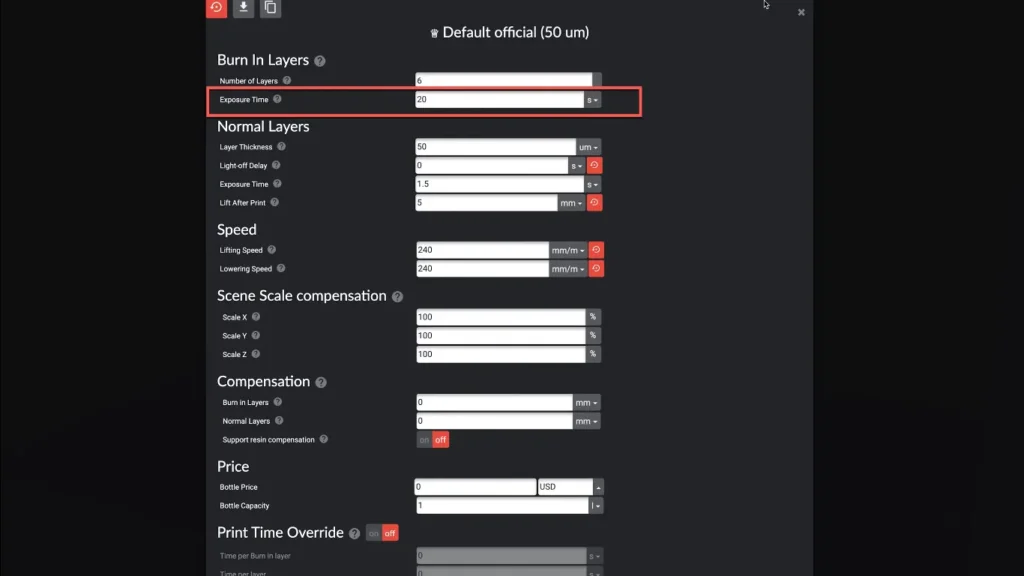
Different slicers call this setting by different names:
- ChiTuBox: “Bottom Exposure Time”
- Lychee: “Burn-In Layer Exposure Time”
- PrusaSlicer: “Initial Exposure Time”
Start by bumping up this setting in small increments – we’re talking 5-10 milliseconds at a time. Keep testing until your prints stick like they’ve been superglued.
Temperature Matters
Resin can be as temperamental as a cat in a bathtub when it comes to temperature. If your printing area is colder than a penguin’s toes, your resin might not be curing properly. Consider wrapping a fermentation belt around your vat if it’s metal, or set up a space heater nearby if it’s plastic. Aim for a cozy temperature that’ll make your resin happy.
Resin Health Check
Just like milk, resin can go bad. If your usually reliable resin suddenly starts acting up, it might be time for a freshness check. Store your resin in a cool, dark place, like a vampire avoiding the sun.
If you’ve had the resin for a while, give it a good stir before use. Sometimes the components can separate, leading to printing issues. And if you’re seeing floaters in your resin, it’s time for a straining session. Use a filter to catch any cured bits that might be sabotaging your prints.

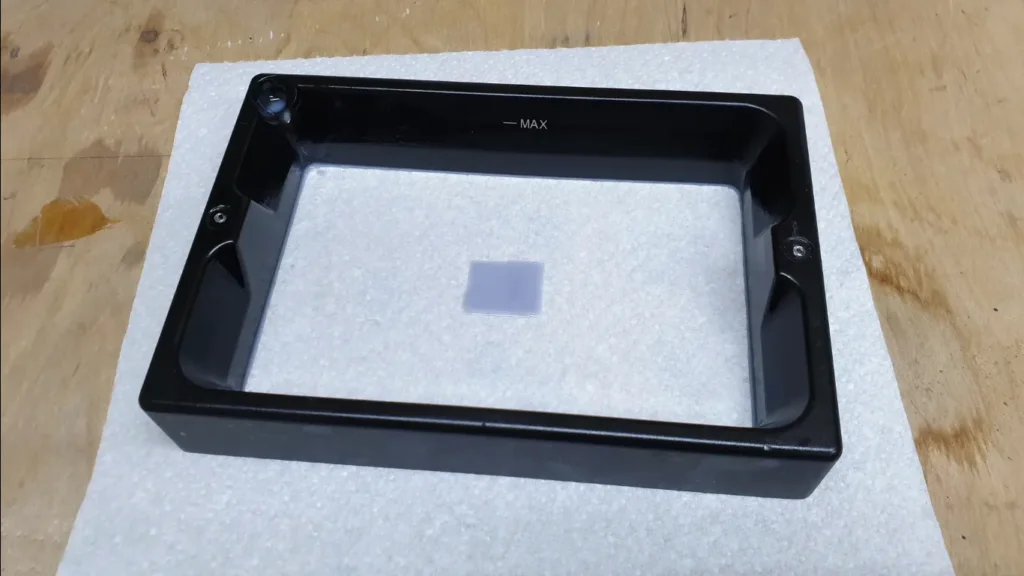
The FEP Sheet Tango
The FEP sheet at the bottom of your resin vat plays a crucial role in your print’s success. If it’s too loose, too tight, or just plain tired, your prints might suffer. Some printers like their FEP sheets tighter than a drum, while others prefer a specific tension. If you’re feeling fancy, you can even use a spectrometer to check the frequency of your FEP sheet – aim for around 320-350 Hz for optimal performance.
Check Your Supports
One critical factor I overlooked is the importance of proper supports. When a print is slowly falling into the resin, it could be due to inadequate support structures. Here’s what to consider:
- Support Density: Ensure you have enough supports, especially for larger or more complex models.
- Support Thickness: Thicker supports provide more stability but can be harder to remove. Find the right balance for your model.
- Support Placement: Pay special attention to overhangs and islands in your model. These areas need extra support to prevent drooping or detachment.
Orientation Matters
The orientation of your model can significantly impact print success:
- Minimize Overhangs: Try to orient your model to reduce large overhangs. This decreases the need for extensive supports and reduces the risk of print failure.
- Angle for Success: Often, angling your model at 30-45 degrees can improve print quality and reduce the suction force between layers.
Resin Viscosity and Mixing
I should have mentioned the importance of resin consistency:
- Shake Well: Always shake your resin thoroughly before use. This ensures all components are well-mixed.
- Viscosity Check: If your resin seems too thick or thin, it might affect print adhesion. Some resins benefit from gentle warming to achieve optimal viscosity.

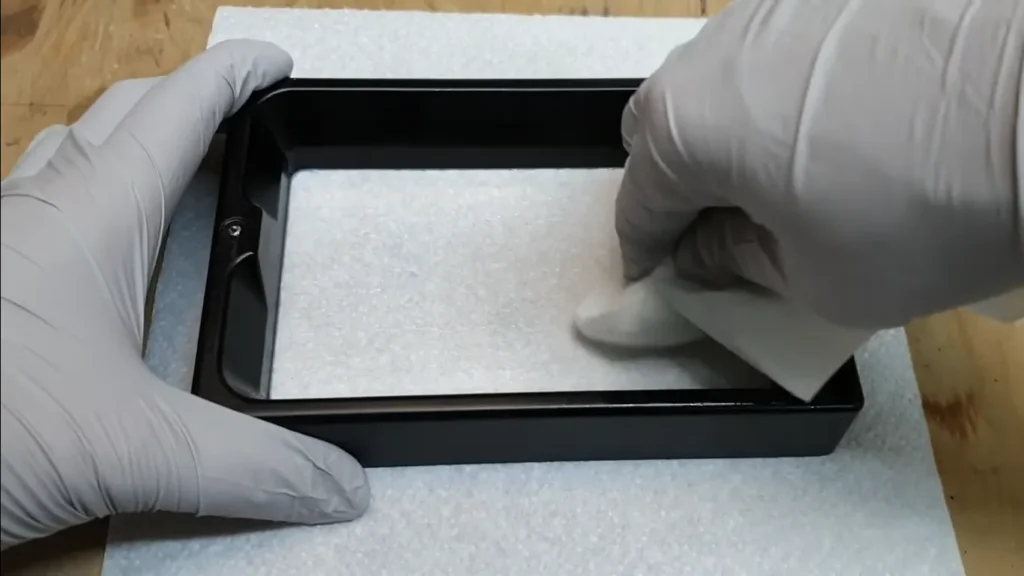
Clean Your Vat and Check for Debris
A clean printing environment is crucial:
- Regular Vat Cleaning: While you don’t need to clean after every print, regular maintenance is important. Check for any cured bits floating in the resin.
- FEP Film Inspection: Look for any scratches or cloudiness on the FEP film that might interfere with proper curing.
Calibrate Your Exposure Settings
I should have emphasized the importance of calibration tests:
- Exposure Test Models: Use specific calibration models designed to help you dial in the perfect exposure settings for your resin and printer.
- Iterate and Adjust: Don’t be afraid to run multiple tests, adjusting settings each time until you achieve optimal results.
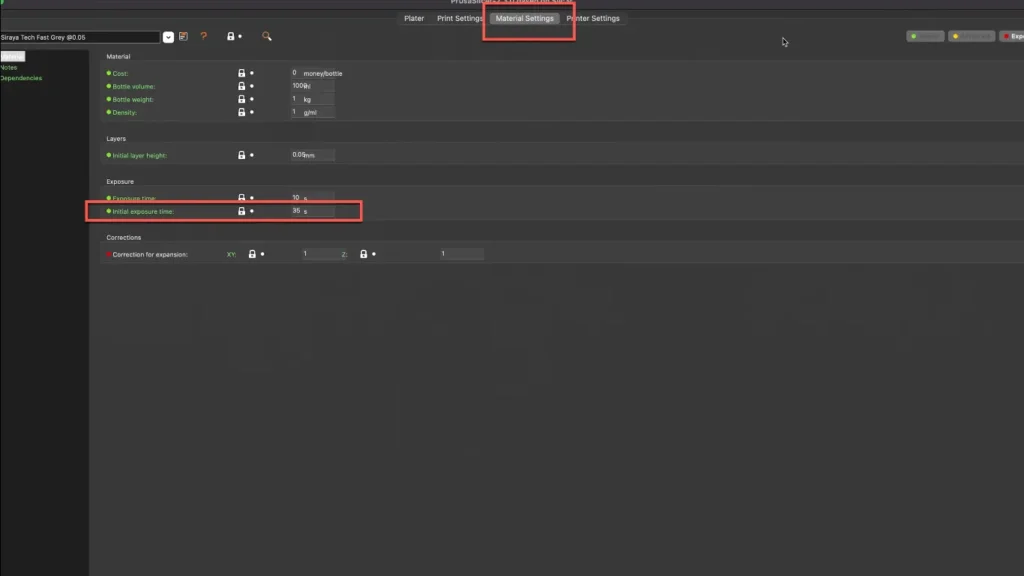
Consider Environmental Factors
Lastly, I overlooked the impact of the printing environment:
- Vibrations: Ensure your printer is on a stable surface. Even minor vibrations can affect print quality.
- Air Flow: Be mindful of drafts or air currents that might affect resin temperature or introduce dust.
When All Else Fails
If your 3D prints keep unexpectedly detaching from the build plate, even after trying everything, it’s time to troubleshoot further. Keep a check on the hardware of your printer if there is any fault UV light or damaged LCD screen. If you are having troubles with them, never shy away from support of the vendor.
Remember, even experienced 3D printers face occasional failed prints. It’s a normal part of the learning process. Keep experimenting and be patient, and you’ll soon be printing successfully and consistently.
Happy printing, and may your resin always cure in all the right places!
FAQs
Help! My print started great but now it’s doing the resin backstroke. What gives?
Don’t panic! This sneaky issue is usually due to poor adhesion or inadequate supports. First, check if your build plate is leveled properly. If it is, try increasing your bottom exposure time and beefing up those supports. Remember, sometimes a little extra support goes a long way in keeping your print high and dry.
I’ve tried everything, but my prints keep taking a dip. Could it be my resin?
You might be onto something there, Sherlock! Old or contaminated resin can be a real party pooper. Give your resin a good shake (with the cap on, unless you fancy a impromptu Jackson Pollock), and make sure it’s not past its prime. If it’s looking a bit funky, it might be time for a fresh bottle.
My build plate looks cleaner than my dinner plates. Why won’t prints stick to it?
Ah, the old “too clean to function” dilemma. Believe it or not, a little roughness can actually improve your 3D prints. Try gently sanding your build plate with high-grit sandpaper. This will create a slightly textured surface that can help your prints adhere better. This creates a subtle texture that gives your prints something to hold onto. Just don’t go overboard – we’re aiming for a light scuff, not a canyon.
Is it normal for the first few layers to look like a pancake?
Absolutely! Those first layers are crucial for adhesion, so they’re often a bit overexposed. This “elephant’s foot” effect is normal and usually gets trimmed off in post-processing. If it’s excessive, you can dial back your bottom exposure time a smidge, but don’t go too far or you’ll be back in Sinky Town.
I heard temperature matters. Should I knit a sweater for my printer?
While a tiny printer sweater would be adorable, it’s not quite what we mean. Resin likes to be cozy – usually around 20-25°C (68-77°F). If your printing area is chillier than a polar bear’s toenails, consider using a space heater or a fermentation belt around your vat. Just don’t go overboard; we’re aiming for “comfortable room temperature,” not “sauna.”
My FEP sheet looks like it’s been through a war. Time to replace?
If your FEP is looking more battle-scarred than a pirate’s treasure map, it might be time for a change. A cloudy, scratched, or slack FEP can cause all sorts of printing mayhem. When in doubt, swap it out. Your prints will thank you.
I’m tired of playing “Guess the Perfect Settings.” Any shortcuts?
Oh, we feel you on that one! While there’s no magic “perfect print” button (yet), calibration tests are your best friend. Look for exposure test models online – these nifty prints help you dial in your settings without wasting a ton of resin. It’s like a cheat code for your printer!
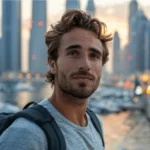
Nikko Jenkins is a technology journalist based in the US, covering tool reviews and comparisons across North America, Europe and Asia, particularly 3D Printers. His concise, insightful articles on the latest innovations help readers worldwide make informed tech decisions. Jenkins’ expertise and engaging style have made him a respected voice in the global technology landscape.
Feel free to reach out to me at nikkojenkins@360techinsights.com.