Austrian scientists developed methods to bond materials without adhesives, potentially revolutionizing manufacturing processes.
Scientists in Austria have developed two groundbreaking methods for joining materials that could revolutionize the manufacturing industry. These innovative techniques create exceptionally strong bonds at the pore level, potentially eliminating the need for traditional adhesives.
Researchers at the Graz University of Technology (TU Graz) have introduced “Addjoining” and “Ultrasonic Joining,” two processes that successfully bond various wood types with plastics, stainless steel, and titanium alloy. These methods offer a promising alternative to conventional adhesives, which often pose environmental and health concerns.
The first technique, Addjoining, utilizes 3D printing technology to directly print materials onto untreated wood. This process allows the printed material to penetrate the wood’s pores, creating a bond similar to that of an adhesive. Gean Marcatto, a postdoc involved in the research, noted that when the bond was broken, “polymer in the wood pores and broken wood fibers in the polymer” were observed, indicating the strength of the connection.
Ultrasonic Joining, the second method, employs high-frequency, low vibration waves to generate friction and heat at the junction of wood and metal polymers. This localized heating creates a precise and strong bond between the materials. Awais Awan, a co-author of the study, highlighted that this technique is “particularly suitable for large components and 2D structures.”
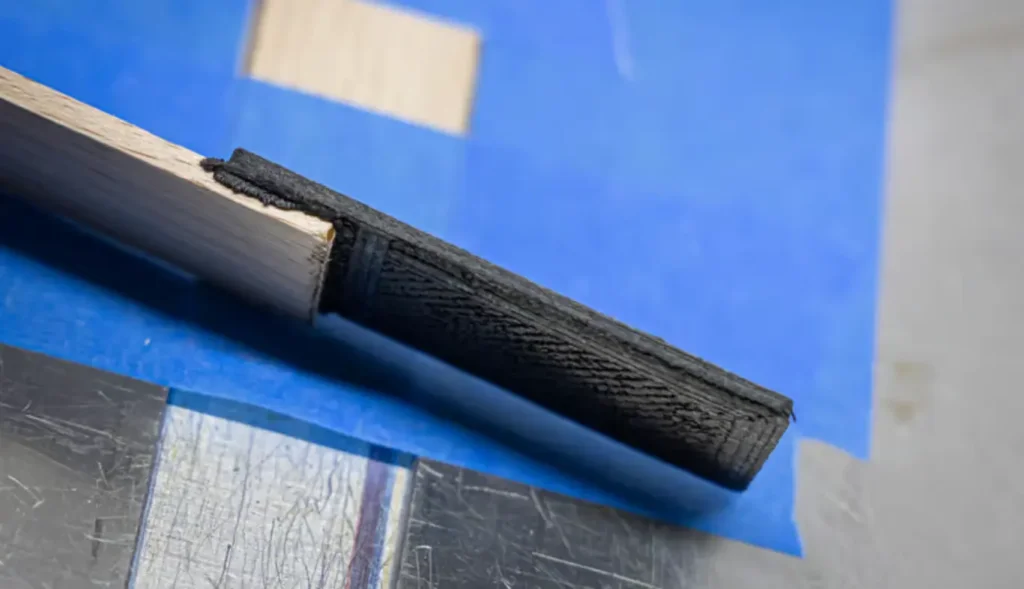
These innovative joining methods could revolutionize industries like furniture, automotive, and aerospace. By replacing traditional chemical adhesives, they offer a more sustainable and environmentally friendly approach to manufacturing.
While the researchers believe these bonds could be further strengthened through additional processes like laser etching, they emphasized their goal of minimizing steps and avoiding chemical use. Sergio Amancio, who led the research, stated, “We can use this technology particularly well with complicated 3D geometries because the components are printed directly onto the surface – in whatever geometry is required.”
As manufacturing continues to evolve, these innovative bonding techniques from TU Graz may pave the way for more sustainable and efficient production processes across multiple sectors.
The findings were presented at the recent IIW Annual Assembly and International Conference on Welding and Joining in Rhodes, Greece, sparking interest in the potential applications of these novel joining methods.
Source: TU Graz
Read more recent news:
- Robust 3D Printing Method Creates Tough, Sticky Hydrogels
- Creality Launches K1 SE: Affordable High-Speed Printing
- Ford Accelerates Electric Explorer Design with Advanced 3D Printing
- Seeed Studio Unleashes Tiny Powerhouse Xiao RA4M1 Microcontroller
- Housing in 48 hours with worlds largest 3D printer from wood
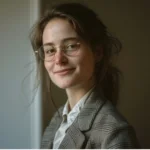
Alexa Sipes is a U.S. tech journalist with 5 years of experience, now writing for 360TechInsights. She covers emerging technologies and industry trends across North America, Europe, and Asia. Sipes’ concise reporting offers readers valuable insights into the latest tech news, innovations and the companies behind them.
Feel free to reach out to me at AlexaSipes@360techinsights.com.